Reduction of SOx Emissions
Slagomite is used widely around the world to help in the reduction of SOx emissions, as it has around 1% Sulfur within its matrix in the form of Sulfides it can be used to dramatically reduce the amount of Sulfate added. The normal procedure of adding a Sulfate source, reducing it with Carbon to form the Sulfides, isn’t needed.
- Slag Sulfide allows a delayed and longer acting reaction between S2- and SO4
- Carbon based systems tend to react earlier
- Allows the reduced redox flint and Float type glasses to be made
- Simpler redox control with a weak reducing agent such as Slagomite
- In many cases the use of Slag will allow a saltcake free stable Amber glass to be made
In Amber glasses we regularly see reductions of 50% in Sox emissions which can in some plants ensure they operate within the legal requirements without the addition on post furnace gas treatment, or ensure that any treatment plant installed is run more economically.
Reduction of CO2 Emissions
The benefits of using Slagomite to reduce CO2 emissions are two-fold, with both direct savings through reducing process CO2 emissions and indirect savings through reduced emissions associated with fuel combustion. As regulation of CO2 emissions increases these reductions will become even more important and valuable.
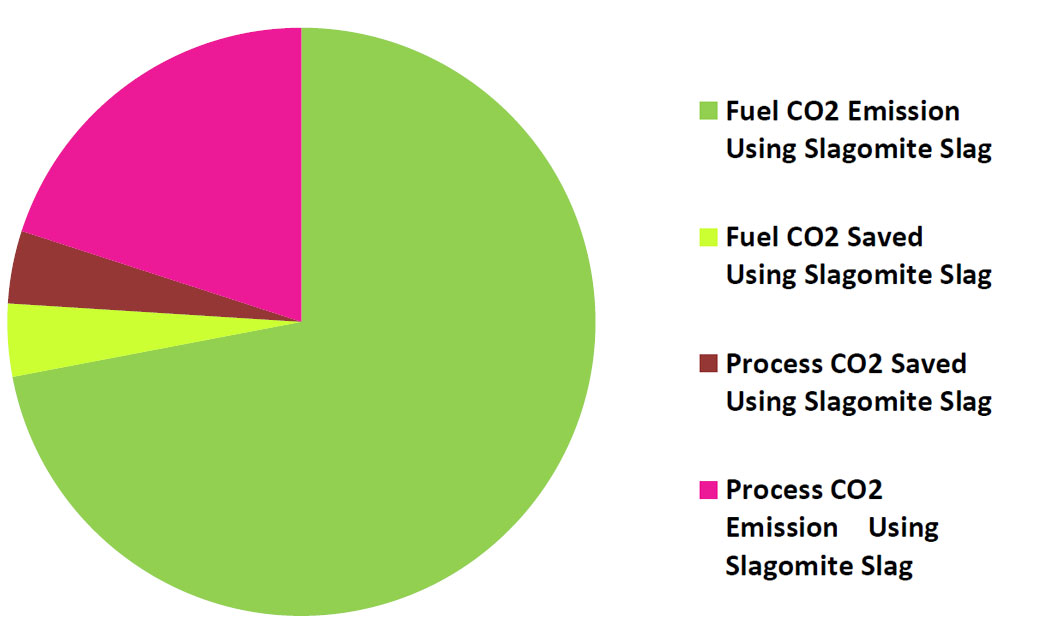
Reduction of Process CO2
The use of Slagomite and partial replacement of limestone and dolomite offers a direct reduction in the evolution of CO2 during the glass melting reactions. Up to 40% of the CaO in the glass can be provided by Slagomite, offering an 18% reduction in process CO2 emissions. This also has the added benefit of reducing the amount of CO2 in the melt which has the potential to form seed or blister defects in the final production glass.
Reduction of CO2 Emissions from Fuel Consumption
The reduced energy consumption through the use of Slagomite results in reduced CO2 released during combustion, whether the furnace is gas or oil fired. In amber and green container furnaces, a 5 - 8% reduction in fuel consumption can be achieved, offering a corresponding reduction in CO2 emissions.
Reduction of NOx
In an air-fired furnace, with approximately 70% of the atmosphere being nitrogen, the rate of NOx formation increases exponentially with temperature. Therefore, reduction in furnace crown temperatures that can be achieved by using Slagomite due to its faster, more efficient melting has a major impact on NOx reduction. The implementation of Slagomite can lead to a 30°C reduction in crown temperature, which equates to a 10% reduction in thermal NOx.
Slagomite Slag Level |
CO2 Saving | |||
---|---|---|---|---|
Process | Fuel | Total | ||
Amber Container | 16% | 18% | 4% | 7% |
Green Container | 13% | 16% | 4% | 6% |
Flint Container | 6% | 9% | 3% | 4% |
Clear Float | 5% | 6% | 3% | 4% |
The levels of CO2 reduction are significant
The use of Slagomite in the batch reduces the quarrying of virgin raw materials, through the partial replacement of limestone and dolomite. In addition, feldspar and nepheline syenite, or other Alumina sources, can be wholly or partially removed from the batch.